Solving guiding problems on forming fabrics
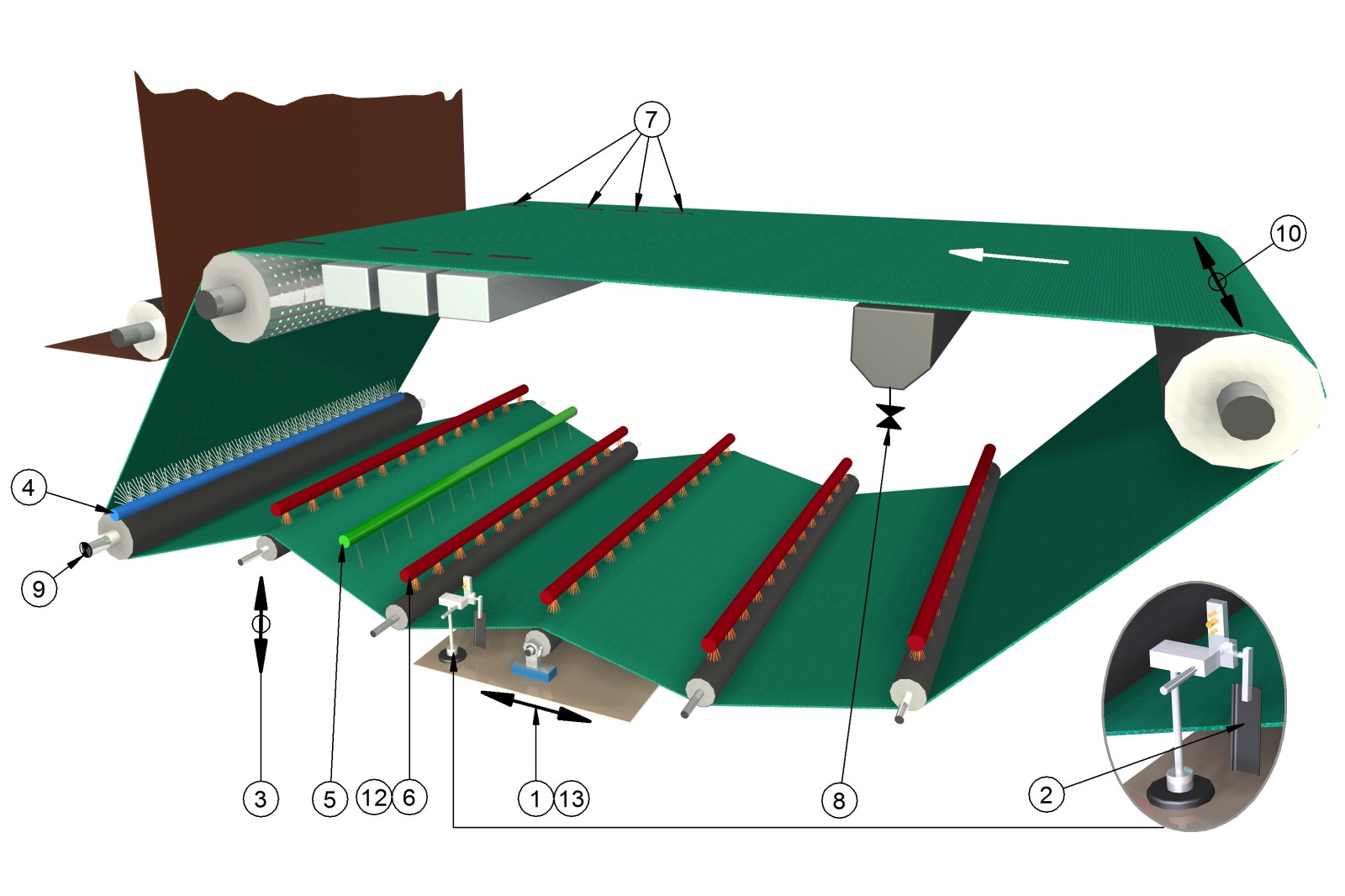
When a forming fabric doesn’t want to run straight it usually causes many problems and costs. In the worst case, it actually runs into the machine frame and the fabric is completely destroyed. But also continuous strong guiding corrections lead to excessive fabric wear and hence high costs. This article explains the principles of forming fabric guiding and gives the papermaker tips on how to systematically solve guiding problems.
The principle of fabric guiding
In the loop of each fabric there is one roll equipped with the task to keep the fabric running straight: the guiding roll. One side of the guiding roll, usually at the tending side of the machine, can be moved in the running direction of the machine
The fabric will always travel toward the side of the guide roll that it contacted first. This is the right hand side or drive side (DS) of the machine. The left edge of the fabric reaches the guide roll first and moves the fabric to the left or tending side (TS) of the machine.
The importance of friction
The friction created between the guide roll and the forming fabric is the key of the guiding process. When one edge of the fabric encounters friction, it will be slowed down a little. This again will generate a cross direction force in the fabric, moving it toward the side with more friction. Please note that this applies for all items contacting the fabric; therefore a misaligned suction box can cause tremendous guiding problems too!
There are several ways to increase the friction on the guide roll:
Increasing the fabric tension;
Increasing the angle of wrap on the guide roll;
Increasing the diameter of the guide roll (thereby increasing the contact area);
Increasing roll softness.
Water reduces friction
Apart from the 4 points mentioned above, another critical consideration in maintaining friction is the amount of water on and around the guide roll. Water acts as a lubricant and when it becomes trapped between the roll and the fabric and it drastically reduces the guide system’s effectiveness.
Since fabric showering is critical to the total paper making operation, showering changes are normally used as a last resort to improve fabric guiding.
Wire tension
As mentioned before, guiding is directly controlled by surface friction between the fabric and the guide roll. Surface friction in its turn is strongly affected by the fabric tension; the higher the fabric tension, the more surface friction and hence a more responsive guiding system.
If experiencing guiding problems, always check for the correct operation tension on your fabric. Check the tension on both sides of the machine (TS and DS) and at the same position, for example before the guiding roll. Tension differences between the two sides are usually related to either misalignments or the forming fabric itself, but should always be resolved.
Be sure that your tension measuring device is giving correct values; see our related article on poorly maintained tension gauges for additional useful information.
Angle of wrap around the guide roll
The larger the angle of wrap around the guide roll, the higher the effectiveness of the guiding system. The minimum wrap angle varies a bit with the length of the fabric. For longer fabrics, like on Fourdrinier machines, a wrap angle of at least 25° (figure 1) is needed to adequately guide a fabric. For shorter fabrics, like top formers or gap formers, it can also be a little less to avoid a hyper-sensitive control system.
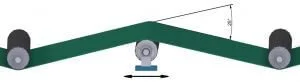
figure 1
Location of the guide roll in the machine
The location of the guide roll on some (older) machines can contribute to guiding problems. When the guide roll is adjacent to the stretch roll, either on the ingoing or outgoing side, the wrap angle will change when the stretch roll moves.
When a relatively short fabric is installed, as in the example in figure 2, the wrap angle will decrease and hence guiding problems may occur. Ideally the guide roll is positioned between two stationary rolls.

figure 2
Guiding roll cover
Roll cover material and its hardness are critical in maintaining adequate friction between fabric and guide roll. Rubber-covered rolls with a hardness of 20 P&J are recommended for guiding today’s fabrics.
However, because rubber rolls tend to harden over time, which reduces the friction between guide roll and fabric, periodic roll grinds are necessary to maintain the correct roll hardness. These rolls typically need to be reground every 2-3 years.
Polyamide yarns in the fabric
In a forming fabric, the yarns in cross machine direction are usually made of polyester and/or polyamide. Polyamide is more wear resistant and helps to increase the fabric life. However, the friction coefficient between polyamide and the guiding roll is about 30% less than with polyester yarns. This means that the previous remarks on tension, wrap angle and roll cover are even more important for forming fabrics with high polyamide content.
Drill and twill patterns
Sometimes a guiding situation occurs where the fabric guides one way with the stock off and in the other direction when the stock is on. This situation is normally caused by one of two possibilities.
Misalignment of a vacuum element.
A misaligned vacuum element will cause the fabric to guide, with the stock off, towards its leading edge. When the stock is applied and the vacuum becomes effective, the fabric tends to guide in the other direction. This usually requires a severe and fast adjustment by the guiding system to keep the fabric running properly. Always check for proper alignment of especially the vacuum elements when this phenomenon occurs.
Drilled suction box covers
If there is no misalignment and the machine has suction boxes with drilled covers, then the latter in combination with the fabric design may cause the guiding problems.
There is a twill pattern in every woven cloth: it is actually the diagonal pattern caused by the cross-over points in the weaving process. When this fabric twill pattern and the suction box drill pattern match, the fabric will have a tendency, when vacuum is applied, to guide in that direction (figure 3).

figure 3
To eliminate the possibility, the best option is to replace the drilled suction box covers with slotted ones. This will not only reduce the guiding problem, but it will also reduce fabric wear and improve the dewatering capacity of the suction box.
If replacing the covers is not possible, the second best option is to alternate the drill pattern angle in successive suction boxes. The last suction box in running direction should have the drill angle opposite to the twill angle of the fabric.
Troubleshooting list for guiding problems
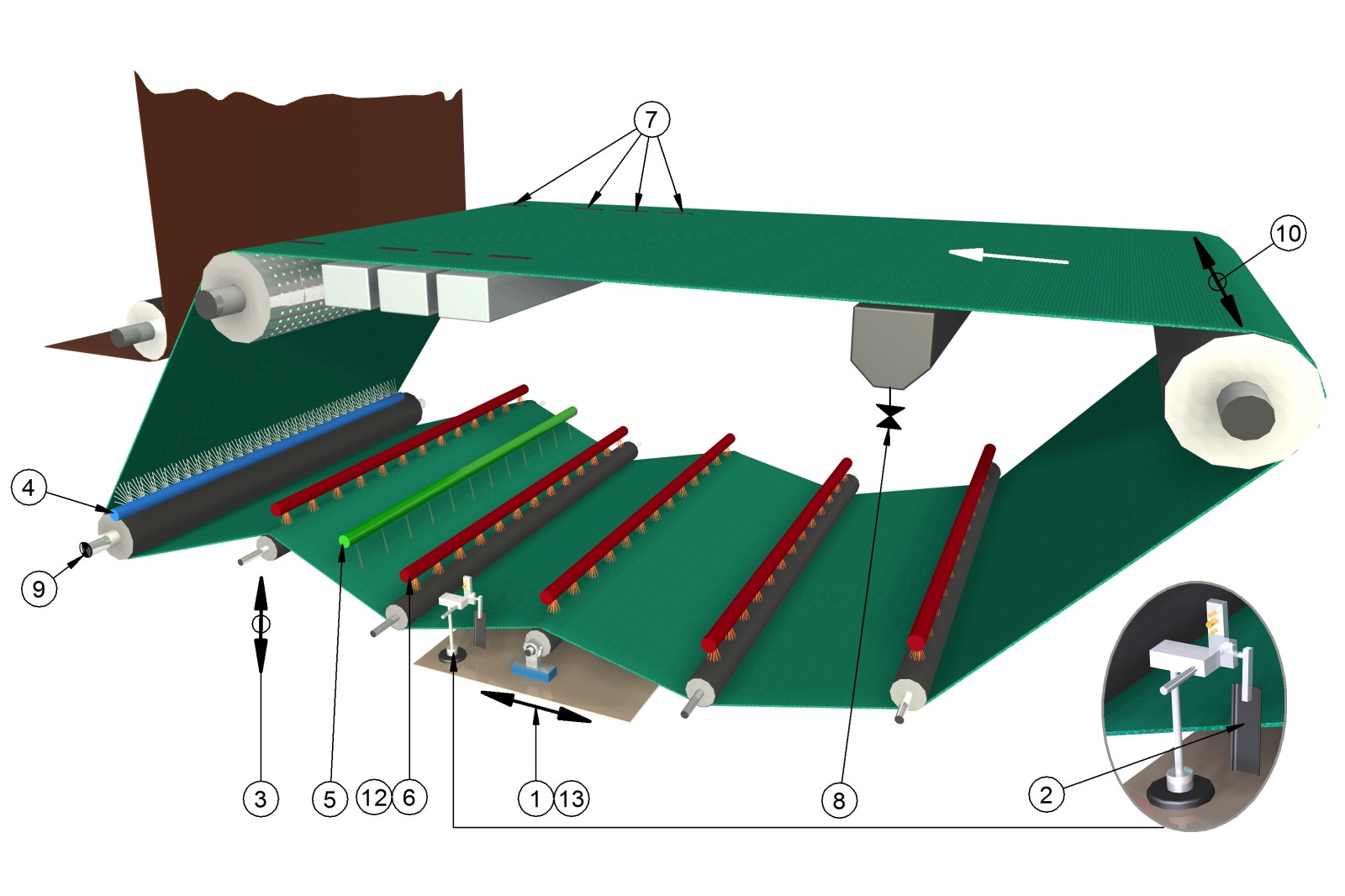
figure 4
Check the guide roll mechanism
Check the function (and position) of the guide plate
Increase the wire tension
Shut off the flooded nip shower and …
… increase pressure of the needle showers
Close or reduce lubrication showers near the guiding roll
Check the suction box deckles, couch roll deckles and pick up roll deckles
Eliminate pumping of the wet box/vacufoil
Reduce power consumption
Check the shaking mechanism
Check the drill and twill pattern (at the last suction box)
Check the water treatment of the lubrication showers
During a stop: check the roll surface of the guide roll (20 P&J)
During a stop: check the alignment of all the elements touching the fabric
This is one of a series of articles on Paper Machine Clothing related topics which can be found in knowledgebase of the Feltest website.