(Part 2/3) Maximize Your PMC - Maximize Your Mill
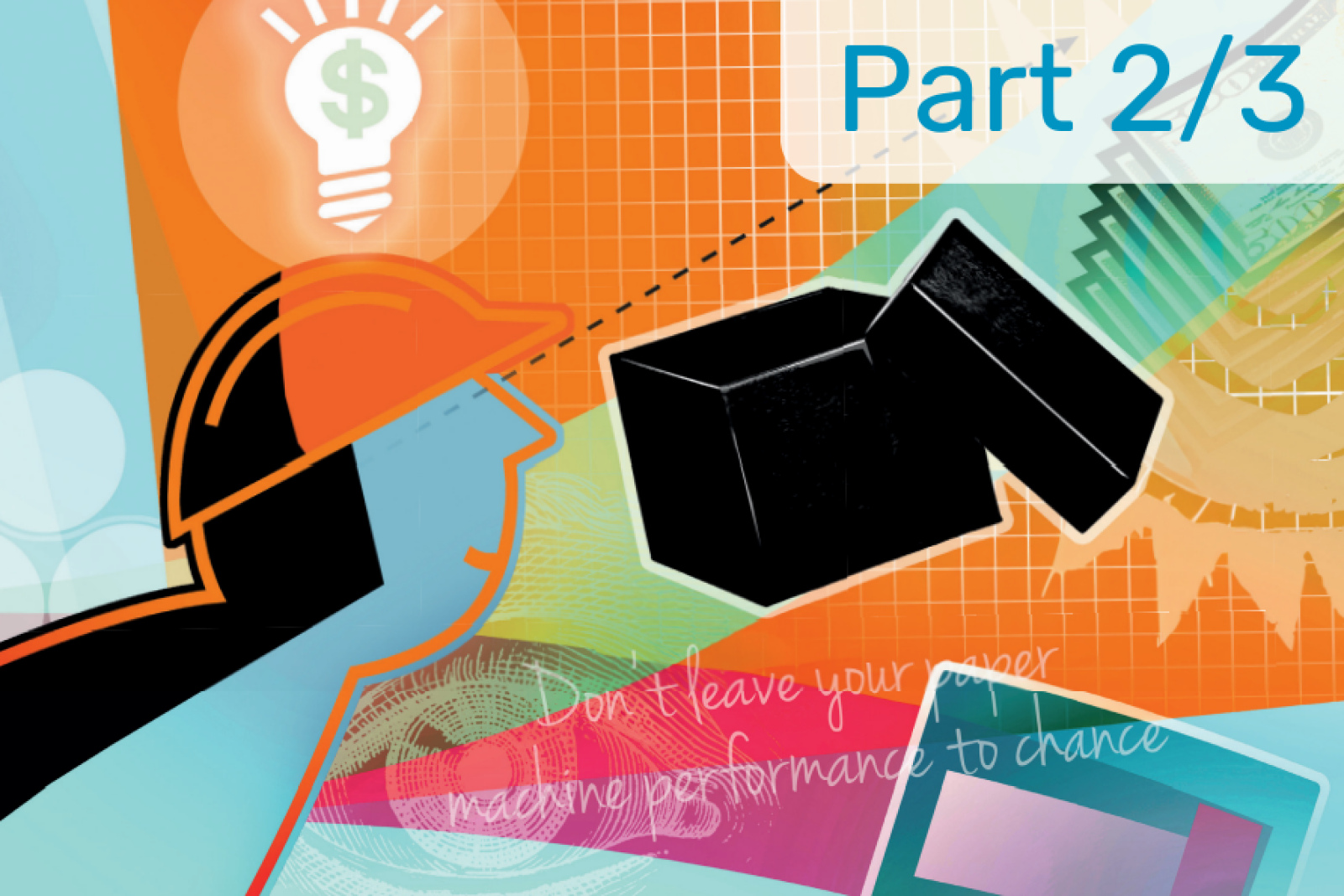
When you focus on innovation, you find ways to get maximum value from your paper machine clothing and in return, future proof your mill.
While PMC tests and trials may seem inconvenient at first, they are highly profitable in the long run.
There are three important principles to consider when running PMC trials, detailed below. As mentioned, all paper machines have their own complexities, so I trust you to recognize how the principles apply to your situation.
1. Focus on the positives—not the problems
Many papermakers see their machine clothing, in combination with a volatile machine, as a complex system. There are many interacting components, where the relationship and interactions between those components make its behavior difficult to predict. It’s this uncertainty that can cause papermakers to leave everything to the supplier.
Instead of only identifying the problem when something goes wrong, spend more time understanding the patterns that appear when your machine is performing well. This is the key to improving its output.
While every machine has its bad days, not all problems appear at the same time. There are always times when the machine is running fine. By understanding these positive moments, we find solutions. Investigate what’s different on the good days compared to the bad.
Psychologically, it’s also nicer to focus on the positives. Problem-led investigations often lead to blame and defensive behavior, whereas people are more cooperative in a solution-oriented approach.
2. Define an target and translate it into money
Patterns appear when comparing the good and the bad times of machine clothing. The bad times may coincide with the break-in phase of a felt, or the end-of-life of a forming fabric, for example. Good times may show less vibrations in the fourth press.
When optimizing a complex system, your production team must focus on just one performance goal. These goals must be measurable, objective, and translatable into money—giving you a clear benchmark to experiment against.
The complexity of a paper machine, the many parameters that influence the total result, is often used as an excuse for not being able to set clear goals and supporting KPIs. Simply ignore the external factors and start measuring and collecting data—then decide what was not relevant.
An example KPI in practice
Let’s use an example of the sheet coming out of the press section 1% dryer. That means higher speeds, fewer breaks, and lower steam consumption. On average, your machine output will increase by 4%, or reduce energy consumption by 3-4% if you prefer to reduce your cost-level.
Just imagine what that would do to your bottom line.
This can be achieved by buying a slightly better variant of the forming fabrics and press felts that you need to buy anyway.
Other example KPIs include:
Break-in time: the maximum number of hours it takes after a felt installation to get back to a certain machine speed. The yield is more production per felt lifecycle.
Amount of steam (in the first dryer section) per ton of paper: this indicates the dewatering efficiency of the forming and press section together. Less steam consumption = money saved.
Time to install fabrics or felts: if the replacement of machine clothing is the bottleneck in your shutdown planning, this could be a perfect KPI. The yield is more production per felt lifecycle.
Keep your goals and KPIs realistic. Discuss the desired target with your current supplier and two or three new suppliers. It is essential that your goal is achievable.
Share knowledge between production and finance
Production managers are more likely to seize opportunities for savings and performance improvement when the financial department makes them aware of real resource prices (and how these prices are determined). Financial experts are also more likely to seize saving opportunities when the production department can give them insight in the production process.
A habit of knowledge sharing between Production and Finance will result in better overall investment decisions—and not just limited to the costs of PMC or PMC trials.
3. Briefing and Selecting the Paper Machine Clothing Supplier
Select only one supplier per PMC trial to keep focus.
Include your current supplier in the selection and give them a fair chance if they’re open to the opportunity. If you show them you're serious about getting the best possible results from your felts and fabrics, you never know how they might surprise you.
At the same time, introducing a new supplier can stimulate innovation and lead to results you may not expect.
How to Bring a New PMC Supplier Faster on to Steam
Your new supplier will not know the ‘normal’ of your machine, so they need a frame of reference. Usually they would create this themselves through months of service measurements. But, time is money.
Your production manager can build this frame of reference by collecting PMC and paper machine datasets during smooth operational periods, helping the supplier understand the specific properties of your paper machine under the normal circumstances.
Because such a smooth period cannot be predicted, only observed, your ever-present machine production staff are in the best position to compose the reference dataset. Under ‘smooth sailing’ conditions, those operators only need a small investment of 20 minutes per day.
Another advantage of the mill composing a proper dataset is that all measurements will be done with one set of instruments, instead of every PMC supplier bringing its own gear, with unknown calibrations and unknown accuracies.
In part three, we’ll share a real example of what happens when a paper mill embraces PMC tests.