Measuring felt permeability: it’s all about baselines
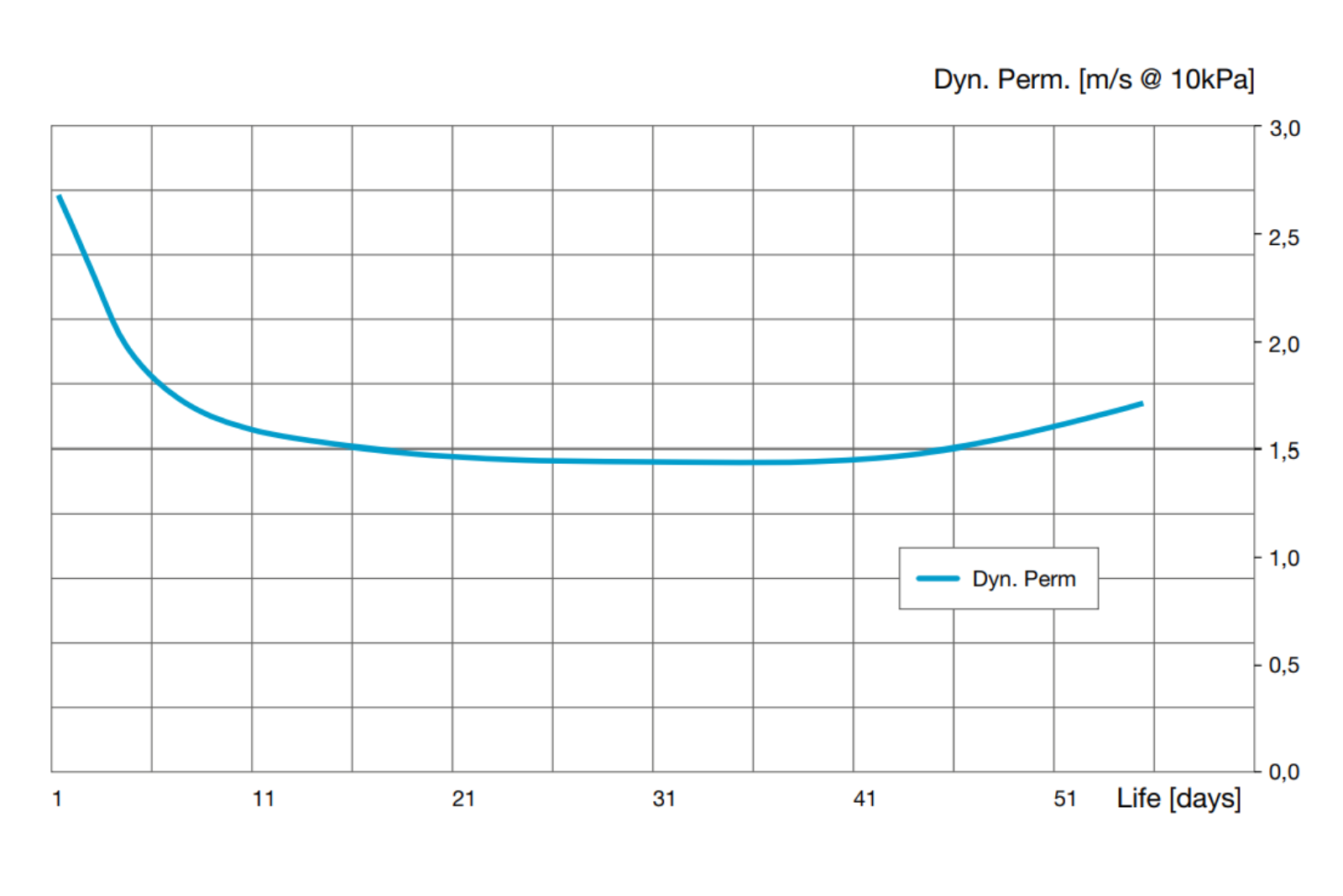
If you’ve read our previous blogs, this statement will come as no surprise: there isn’t a standard, universal metric for ‘correct’ felt permeability. In fact, the only relevant rule of thumb is that machines with nip dewatering require denser felts than those with Uhle dewatering.
This is because achieving optimal permeability is unique to each machine. And it’s determined by two sets of variables. First, the machine’s configuration, such as press and roll cover design, speed, stock quality, and contamination risk. Second, the paper manufacturer’s requirements, such as break-in time, paper smoothness, and minimum felt life.
So how do you find the optimal felt permeability? Well, as is often the case with improving your machine’s performance, it’s a matter of ongoing investigation. Here’s how…
Take regular measurements
Measuring the permeability of your press felts on a regular, consistent basis—for example, every day at 9am—will provide you with objective data for all possible machine conditions. Over time, you will build up a point of reference to help you decide the appropriate action to take.
Felt manufacturers often use instruments such as L&W Feltperm™ or Cristini PermFlowDUO™. These instruments inject pressurized water into the felt and then measure the water flow, but are relatively expensive and rarely used by the pulp and paper mills.
Instead, an easy and affordable way to understand your permeability is to measure how much air the Uhle box draws through the felt. Using an instrument such as the Feltest AirSpeed Sensor will allow you to accurately measure this airflow.
Of course, the measured airflow is closely related to the applied vacuum, so it’s good practice to also record the vacuum in the Uhle box. The Feltest RealVac is a handy portable manometer for measuring directly inside the Uhle box, rather than having to use the usually defective manometers installed on the paper machine.
Dynamic permeability indicator
To easily compare multiple measurements over time, it’s best to have a single indicator that takes into account both airflow and the applied vacuum.
When airflow is divided by the applied vacuum the result is a ‘Dynamic Permeability Indicator’. Once you start monitoring the dynamic permeability on a daily basis, you will be able to extract a baseline like the below table, where although the measured airflow remains constant, the felt becomes denser as the vacuum increases.
On the X-axis you see the felt life in days and on the Y-axis to the right the dynamic permeability in m/s @ 10 kPa.
During the first 5 days of this felt’s life you see a sharp drop in permeability. The felt is still in its start-up phase and is compacting a little more with every revolution. Near the end of its life, permeability increases due to felt wear.
And it’s as simple as that. Measuring felt permeability is all about creating baseline data so you can spot patterns and predict how permeability changes over the felt’s lifetime.