How to design high-performing press felts

Math, science, art? You decide.
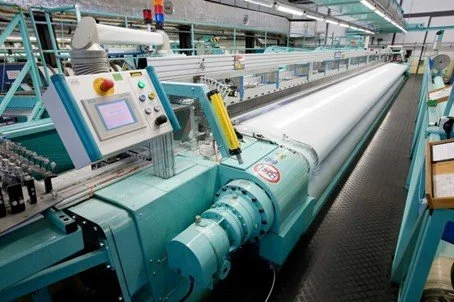
There’s one single truth at the center of this complexity: every felt fabric design is unique.
Dimensions vary between machines and press positions, so the designer must optimize each element of the felt—the base, the batt, the needling, and the finishing—to perform on a particular position of a particular machine.
For a deeper understanding, let's look at each element in more detail. As we do, you’ll see that trying to calculate the number of possible product variations is like trying to calculate the spacetime continuum—an endless task that’ll have your brain folding in on itself. Yet the felt designer must still make these decisions, with the papermaker’s best interests at heart.
The base
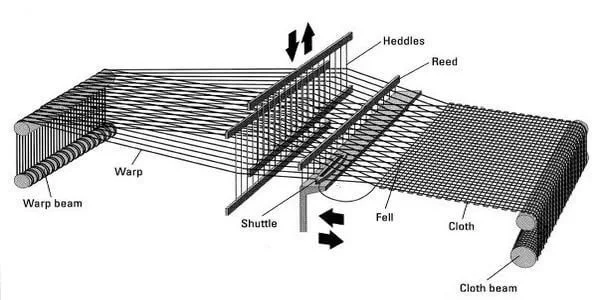
All press felts start with the base; a combination of warp and weft yarns, weaved together on a loom. Warp yarns travel in the production direction of the loom, while weft yarns travel over and under the warp yarns.
A single layer fabric has one layer of warp yarns, while a double layer has two. With double layer fabric, you choose different weaving patterns (shown below) for the top and bottom layer, depending on the characteristics you need.
For added complexity, there are also laminated felts. These consist of two base weaves fixed together by the needling process (which we’ll come to later). The yarn used in these base weaves varies in material, shape, and size (as seen below), so soon enough, a felt supplier has 50 or more base weave designs to choose from. Yikes.
The batt
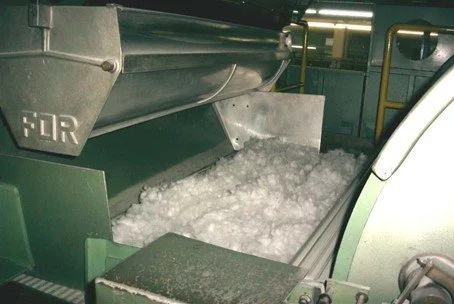
The batt is the soft cover you see on every press felt. In its basic form, it looks like cotton wool, but it’s actually made of thin polyamide fibers.
These fibers come in different grades of fineness, expressed in dtex—the weight (in grams) for 10000m of a single fiber. Press felts commonly use ten different grades: 3, 5, 7, 11, 17, 22, 30, 44, 67, and 100 dtex. The higher the number, the heavier and thicker the fiber.
The coarsest batt fibers sit on top of the base weave, and finer fibers towards the paper side. The felt designer can experiment with the number of layers (e.g. three layers: 67 dtex + 22 dtex + 5 dtex), and also the weight per layer. This again makes the number of possible combinations endless.
Needling
.png)
Once the felt designer has decided which base fabric to use and the layers of batt to apply, these components are fixed together by the needling process.
The first layer of batt is put on top of the base fabric, and then barbed needles punch through, dragging the batt into the base fabric.
As with each step so far, the needling process offers many options for the felt designer to choose from. The density of the needles (how many needles per m2), how deep they punch, how many punches per m2 of felt, the barb of the needle, and needling direction (starting at the paper side or the roll side of the felt) all have their own pros and cons.
.png)
A higher needling intensity, for example, could improve the batt anchorage—which helps prevent felt wear—but at the cost of damaging the base fabric.
Finishing
When the felt is ready—with the layers of batt needled into the felt—it’s time to think about the finishing of the felt. Again, the designer has decisions to make, this time regarding pre-compaction, surface treatment, and chemical treatment.
For high speed machines running with nip dewatering, higher pre-compaction will give a faster startup of the felt. For slower machines, a lower pre-compaction can extend the felt’s life.
Depending on the chosen needling procedure, more or less batt fibers stick out and need to be smoothened. This is done either by calendaring, or by a far more exciting sounding process—scorching.
And finally, the felt designer must decide on the chemical treatment. Every supplier has its own proprietary treatments that improve the startup behavior, sensitivity to contamination, or other features.
Math, science, art—did you decide yet?
If you made it this far, well done. As you can see, there are an exhausting number of permutations possible when designing a press felt. But my goal isn’t to confuse you. Instead, it’s to shed light on the many decisions that go into felt fabric design—and the painful truth that even with the best intentions, there may still be a better variant of press felt possible than the one produced.
As things stand, if a felt trial is not immediately perfect, it’s easy to get discouraged and revert back to the status quo: sticking with existing PMC designs, for fear of further failed tests. But hopefully, with a little more understanding of the process—and with more data collected on the performance of PMC clothing—we’ll have more courage for innovation.