How measuring felt thickness revolutionized nip dewatering
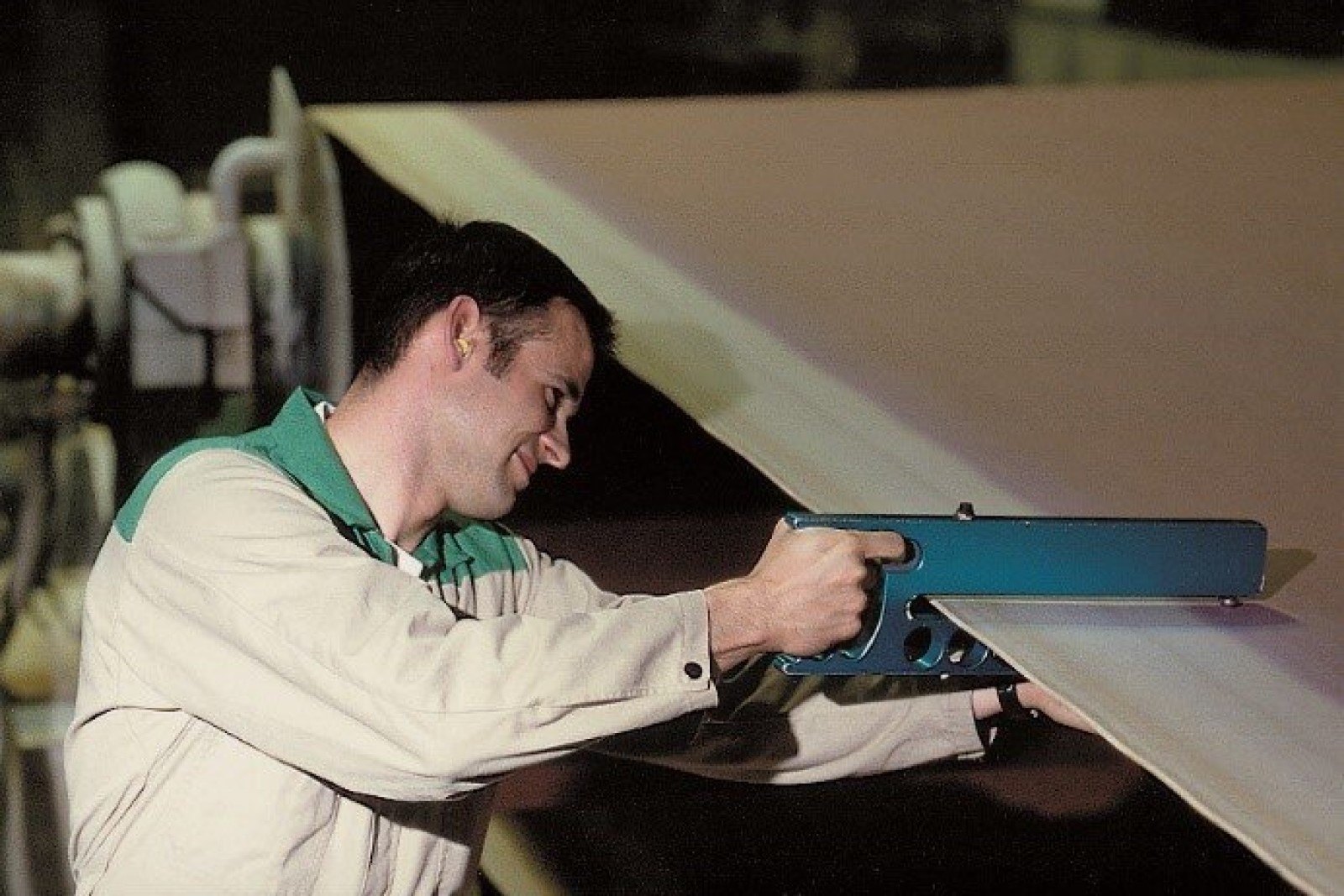
Back in the 1980’s the performance of press felts was mainly judged by looking at the sheet; nobody really knew what was happening inside the felt once it was running. With the introduction of nip dewatering the felt designers needed more information.
A thick, bulky press felt is not a good thing. At least, not when you are running with nip dewatering. In this blog post I tell more about the relation between nip dewatering and the Feltest CaliperProfiler.
NIP Dewatering accelerated by the Caliper Profiler
The CaliperProfiler was Feltest’s first product ever. Actually, it was the spark that started the founding of Feltest as a company!
Back in the 1980’s my father, Nick Lensvelt, was a felt application engineer for one of the world’s leading Paper Machine Clothing manufacturers in Europe. In those old days the performance of press felts was judged only by looking at the sheet. After installation, felt properties were no longer measured or monitored; nobody really knew what was happening once the felt was running.
The introduction of NIP dewatering
It were also the days that grooved press rolls were introduced: the introduction of nip dewatering! With nip dewatering a new question arose: why do felts have a startup or break-in period? My father has a very analytical background and not only wanted to see WHAT happened with the felt, but he also wanted to understand WHY. The only tools available, the Scanpro© Jetmem and the vacuum level on the Uhle box, where not giving him the information he needed to solve this puzzle.
The first in measuring felt thickness on the fly
He designed an instrument that could accurately measure the thickness of a running felt. With its pistol-like handgrip it drew quite a bit of attention.
With the new information the instrument supplied, it became very clear to my father that the mid-nip caliper is an extremely important felt property. Thinner felts with an optimized base weave had less flow resistance in the mid-nip and once the water was out of the nip, rewetting was no longer an issue. These findings resulted in thinner felts that generated more nip dewatering, less contamination, shorter break-in periods and higher sheet dryness. The productivity of paper machines with nip dewatering increased considerably!
In the early nineties Nick Lensvelt accepted a position with another PMC manufacturer. This new company had no intention to start manufacturing measuring gear as well, so it was agreed that Nick Lensvelt would manufacture it himself and the PMC manufacturer would buy it from him. With all his experience from the first model, Nick started sketching an improved version and asked me to do the engineering work. My father and I still had to think of a name for our new established company. I didn’t lose much sleep over that: the instrument is developed for a “felt test”, but then a bit more stylish, so “FelTest” was born!
The first Feltest Caliper Gauge was sold in 1992
In 1992 we supplied the first instrument to this European PMC supplier and, as they say, the rest is history. Nowadays Feltest has sold hundreds of pieces of the classic Caliper Gauge and today’s CaliperProfiler all over the world. Nick Lensvelt’s bright idea, back in the eighties, for sure contributed to the success of the concept of nip dewatering felts. It enabled him and many other felt application engineers over the world to study the effect of felt compaction and to differentiate compaction from contamination. For more details on this, check our whitepapers or watch my presentation at Papercon2018:
The CaliperProfiler as foundation of quality measurement today
For me personally, designing the caliper gauge in 1992 was the start of a successful cooperation with my dad that lasted over a decade until he retired. It was the start of Feltest Equipment BV, today offering a wide range of innovative handheld products to satisfied customers in over 70 countries.
The Feltest Caliper Profiler is a unique and high quality product based on decades of innovation, which enables papermakers to make fact based decisions and to get the best possible performance of their press felts! So if you want to increase nip dewatering, reduce the break-in period or save on the felt life, feel free to get your quote here.
So remember DDPP - Daily Data Powers Production.
Toward better Paper Machine Clothing,
Marcel