There are different ways of saying the sheet doesn’t go where it needs to go in the Press Section:
“Edge stealing” happens at a nip exit. The sheet edge sticks to the felt, where the main sheet is supposed to follow the granite roll.
“Sheet stealing” also happens at the nip exit, but the sticking is not limited to the edges.
“Edge flipping” happens when the sheet (edge) of the felt comes loose. Sometimes the sheet flips over, moving through then next nip as a double layer sheet.
“Blowing” is a different expression for “Edge flipping”.
The most common expression I hear is Sheet stealing.
I have 5 tips to prevent sheet stealing. Before I share my tips, you need to know that the sheet always follows the smoothest surface.
5 Tips To Prevent Sheet Stealing
Reduce water content of the felt
A felt must carry enough water into the nip to create sufficient mid-nip hydraulic pressure. If there is too much water on the felt surface at the nip exit, the felt becomes so smooth that parts of the sheet will stick to the felt. Reduce the inflow of conditioning water, increase the Uhle box vacuum to bring down the felt moisture content.
Clean the felt
When felts are contaminated with fines and fillers, the felt surface will become too smooth. A proper felt wash will help. Read our whitepaper on the correct felt permeability and discover the difference between contamination, compaction and felt wear.
Vary the positions of the suction zones in vacuum supported rolls
I invite you to play with the positions of the suction zones and their vacuum levels. And try the following suggestions that may feel counter intuitive:
Gradually vary the vacuum level. Start with a minimum (or no!) vacuum and increase it in little steps.
Step-by-step rotate the suction zone to the maximum positions in both directions from headbox to pope reel.
For vacuum supported rolls with a additional edge zone: move the vacuum zone step-by-step from the outside to the inside. Don’t mix b. and c.! First find the optimum angle in running direction and only after that start looking for the optimum in axial direction.
Shave the felt
This is the most unconventional advice, but it is simply too much fun to be left unmentioned. As the sheet always follows the smoothest surface, sometimes people try to roughen up the felt surface with a steel wire brush. I strongly recommend NOT to do this!
What happens is that the brush pulls the batt out of the base. Not much later you’ll be facing ‘felt hair’ complaints, or the pulled out batt fibers create an even smoother surface than before, only increasing the sheet stealing problems. Under these circumstances it could be worth a try to buy a set of disposable razors and simply shave the affected area of the felt. On the fly, apply only little pressure and… no shaving foam please!
Related to this: blowing before 3rd and 4th presses can be caused by a rough felt surface that drags air along, which prevents the sheet from lying flat onto the felt. Also then it is worth a try to shave the felt a little.Change the felt exit angle
The felt works as a mini vacuum box pulling at the sheet. Because after passing the mid-nip, the expanding felt sucks in air to fill its growing (void) volume. And if the roll-side of the felt is blocked, the felt will suck in air from the paper side, creating a mini-vacuum zone on the felt surface. To avoid this, let the felt follow the sheet a bit longer. Raising the felt guiding roll after the nip by 4 to 6 inches (= 10 to 15 cm) could already do the trick, as you can see in the example below.
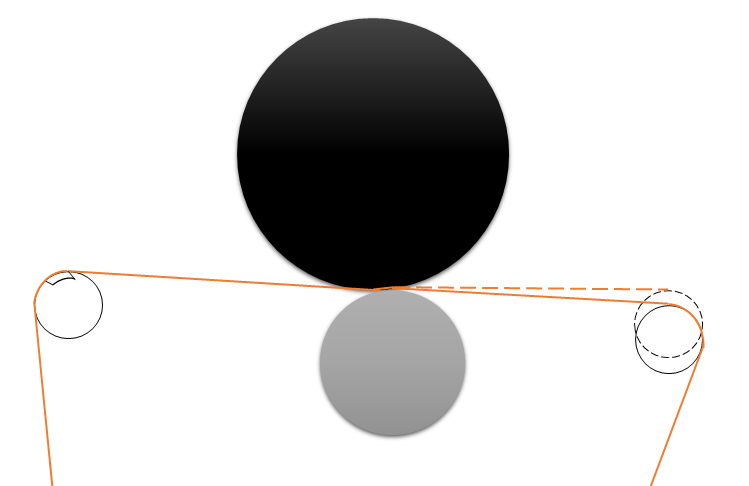
I trust you will benefit from these 5 tips to avoid sheet stealing from our extensive Feltest trouble shooting guide.
I like to close by pointing out that you need to collect daily Paper Machine Clothing data when the machine is running well without problems.
Only when you have data of a good day, you will know how to correct on a bad day.
Contact your felt supplier to learn the impact of a modified felt design on sheet stealing. Make sure you can provide your felt supplier with sufficient daily sheet performance data to avoid bad, costly modification decisions.
So remember DDPP - Daily Data Powers Production.
Toward better Paper Machine Clothing,
Marcel